Tundish spray equipment
With the continuous development of the metallurgical industry and the diversification of production needs, tundish spray equipment have also begun to show a trend of diversification and customization. Different models of gunning machines are suitable for different types of tundishes and refractory materials, and can meet the specific needs of different production lines. At the same time, we also provide customized services, designing and manufacturing according to the specific requirements of customers to ensure the best performance and adaptability of the gunning machine.
Tundish spray equipment is used in steelmaking processes, specifically in continuous casting operations. A tundish is a container that holds molten metal before it is poured into molds for casting. The purpose of the tundish spray equipment is to improve the flow and quality of the molten metal by controlling the temperature, reducing turbulence, and preventing oxidation.
Tundish spray equipment key functions:
1. Temperature Control: The equipment helps maintain the molten metal at the desired temperature to ensure consistent casting quality.
2. Cooling and Lubrication: It typically sprays a cooling agent (like water or mist) onto the tundish or the metal surface, which helps to keep the molten metal in a stable state and prevents it from solidifying prematurely.
3. Prevention of Metal Oxidation: By applying the spray to the tundish and metal, it reduces the exposure of the molten metal to the air, which minimizes oxidation and ensures higher-quality steel.
4. Flow Optimization: The spray system helps regulate the flow of molten metal from the tundish to the molds, preventing issues like slag buildup or turbulence, which can cause defects in the cast steel.
5. Preventing Clogging: It helps avoid the clogging of the tundish by controlling solidification and temperature variations.
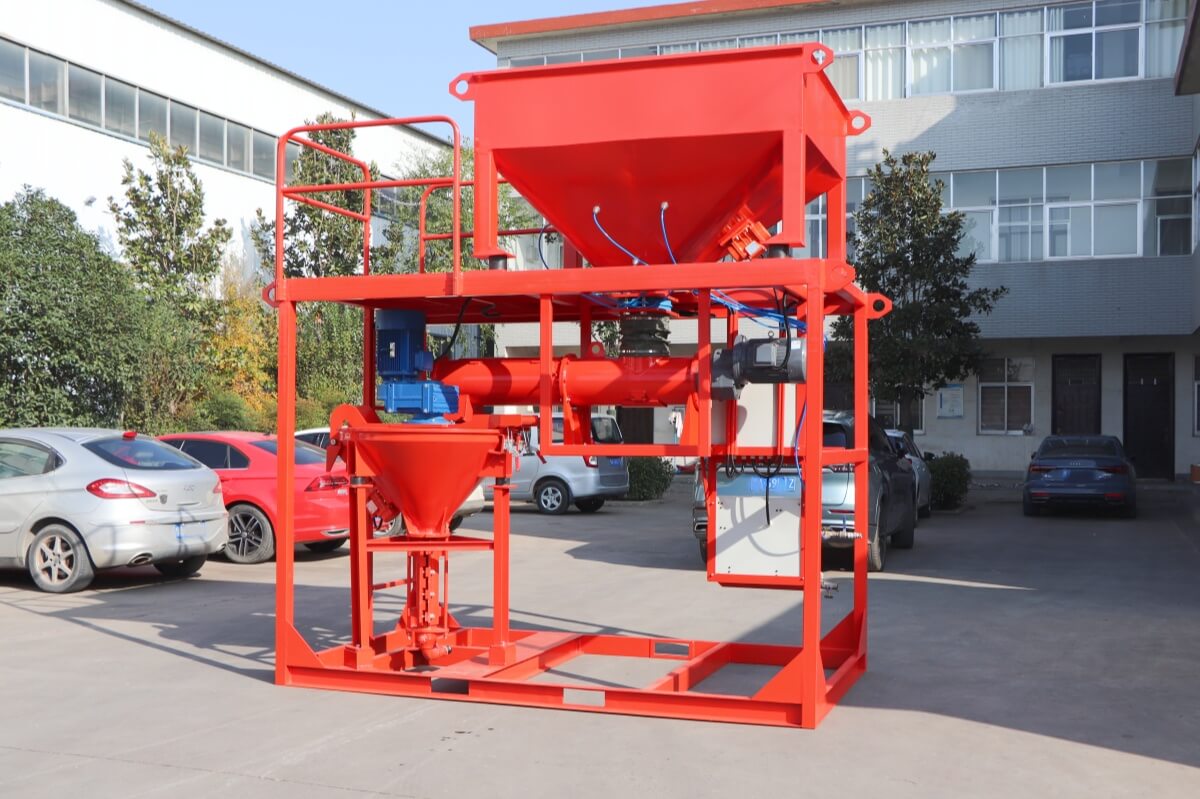
The tundish is an important part of the continuous casting process. It is located between the ladle and the crystallizer and serves as a container for the transition of molten steel. The following is a detailed introduction to the tundish:
1. Definition and function
Definition: The tundish is a container made of refractory material, which is used to receive the molten steel poured from the ladle and distribute it to each crystallizer.
Function:
Diversion effect: For multi-stream continuous casting machines, the tundish diverts the molten steel through multiple water nozzles to ensure that the molten steel can flow evenly into each crystallizer.
Continuous casting effect: When multiple furnaces are continuously cast, the molten steel stored in the tundish plays a connecting role when the ladle is replaced to ensure the continuity of the casting process.
Decompression and stabilizing flow effect: The liquid level of the tundish is lower than that of the steel ladle, and the change range is small, which helps to stabilize the molten steel casting process and reduce the scouring of the solidified shell of the crystallizer by the steel flow.
Protective effect: Through the covering agent of the tundish liquid surface, the long water nozzle and other protective devices, the molten steel is reduced from external pollution.
Purification of molten steel: As the last refractory container before the solidification of molten steel, the tundish helps to further float the inclusions in the molten steel and improve the quality of the molten steel.
2. Structure and material
Structure: The tundish is usually composed of a shell welded by steel plates, and its lining includes an insulation layer (insulation layer), a permanent layer and a working layer. In recent years, in order to increase the service life, a thick layer of alkaline refractory coating is often sprayed on the working layer.
Material:
Insulation layer: It is close to the steel shell of the tundish, and its main function is to keep warm and reduce the temperature drop of the molten steel during the pouring process. Commonly used materials include asbestos boards, insulation bricks or lightweight castables, and the best effect is aluminum silicate fiber felt.
Permanent layer: It is in contact with the insulation layer and plays a role in further insulation and safety protection.
Working layer: It is in direct contact with the molten steel and is a key part. The material is required to have good refractoriness, high temperature strength, chemical stability and anti-scouring performance. The working layer material has gone through the development process of refractory clay bricks, insulation boards, spray coatings (painting materials) and dry vibration materials.
3. Capacity and shape
Capacity: The capacity of the tundish is generally 20%~40% of the steel ladle capacity, and must be greater than the amount of molten steel poured during the replacement of the ladle to ensure the smooth progress of multi-furnace continuous casting.
Shape: The tundish has various shapes, and the common ones are rectangular and triangular, etc., to meet different production needs.
4. Development trend
With the development of metallurgical technology, the functions and effects of the tundish have been continuously expanded and improved. For example, by installing porous air-permeable bricks at the bottom of the tundish or embedding a porous tubular gas distributor between the working layer and the permanent layer for argon blowing, it can promote the removal of inclusions and improve the cleanliness of the molten steel. In addition, the capacity of the tundish is also gradually developing towards large-scale, so as to prolong the residence time of the molten steel in the ladle, which is conducive to the floating of inclusions and the stability of the molten steel temperature.
In summary, the tundish plays a pivotal role in the continuous casting process, and its structure, material, capacity and shape are designed to meet production needs and improve the quality of molten steel.
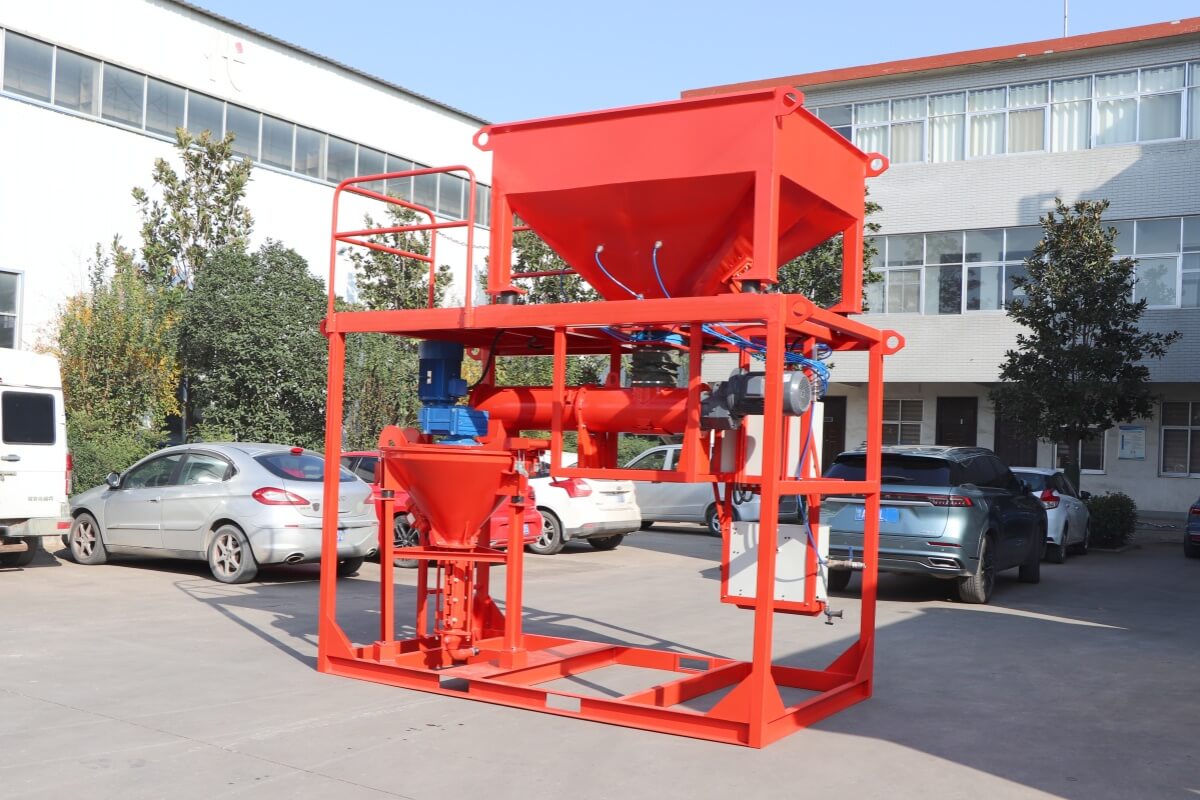
The importance of the tundish spraying gunning equipment to the tundish is self-evident, which is mainly reflected in the following aspects:
1. Maintaining the integrity of the tundish lining
The lining of the tundish is a key part to protect it from the erosion of high-temperature molten steel. During the continuous casting process, the lining of the tundish will gradually wear out due to long-term high-temperature exposure and erosion by molten steel. The tundish gunning machine can quickly and evenly spray refractory materials on the worn parts, thereby repairing and maintaining the integrity of the lining. This not only extends the service life of the tundish, but also ensures its stability and safety during the continuous casting process.
2. Improve molten steel quality and production efficiency
The tundish gunning machine can effectively reduce the interaction between molten steel and refractory materials by precisely controlling the amount and position of sprayed refractory materials, thereby reducing the risk of molten steel being contaminated. At the same time, the rapid spraying capability of the gunning machine shortens the repair time and improves production efficiency. This means that during the continuous casting process, the tundish can be replaced faster, reducing production interruptions, thereby increasing overall output.
3. Adaptability and flexibility
The tundish gunning machine is usually equipped with advanced control systems and mobile devices, which enable it to be flexibly adjusted according to the shape, size and spraying requirements of different tundishes. This highly adaptable feature ensures that the gunning machine can be widely used in various metallurgical production lines to meet different production needs.
4. Reduce costs and resource utilization
The use of the tundish gunning machine can significantly reduce the consumption and waste of refractory materials. Precise spraying ensures that the refractory materials are fully utilized and reduces unnecessary material costs. In addition, extending the service life of the tundish also means reducing the frequency of replacing the tundish, thereby reducing the costs associated with replacement.
5. Improve the safety of the working environment
In high-temperature and high-risk metallurgical environments, manual application of refractory materials poses safety hazards such as scalding and poisoning. The mechanized operation of the tundish gunning machine reduces the direct contact between workers and the high-temperature environment and improves construction safety. At the same time, the automation and remote control functions of the gunning machine also further reduce the labor intensity and safety risks of workers.
In summary, the importance of tundish spraying equipment to tundish is reflected in maintaining the integrity of the lining, improving the quality of molten steel and production efficiency, adaptability and flexibility, reducing costs and resource utilization, and improving the safety of the working environment. It is one of the indispensable and important equipment in the metallurgical industry, and is of great significance to ensure the smooth progress of the continuous casting process and improve the overall production efficiency. If you have the same need about the tundish spraying machine equipment, please contact us by email, email address: sales1@leadcrete.com
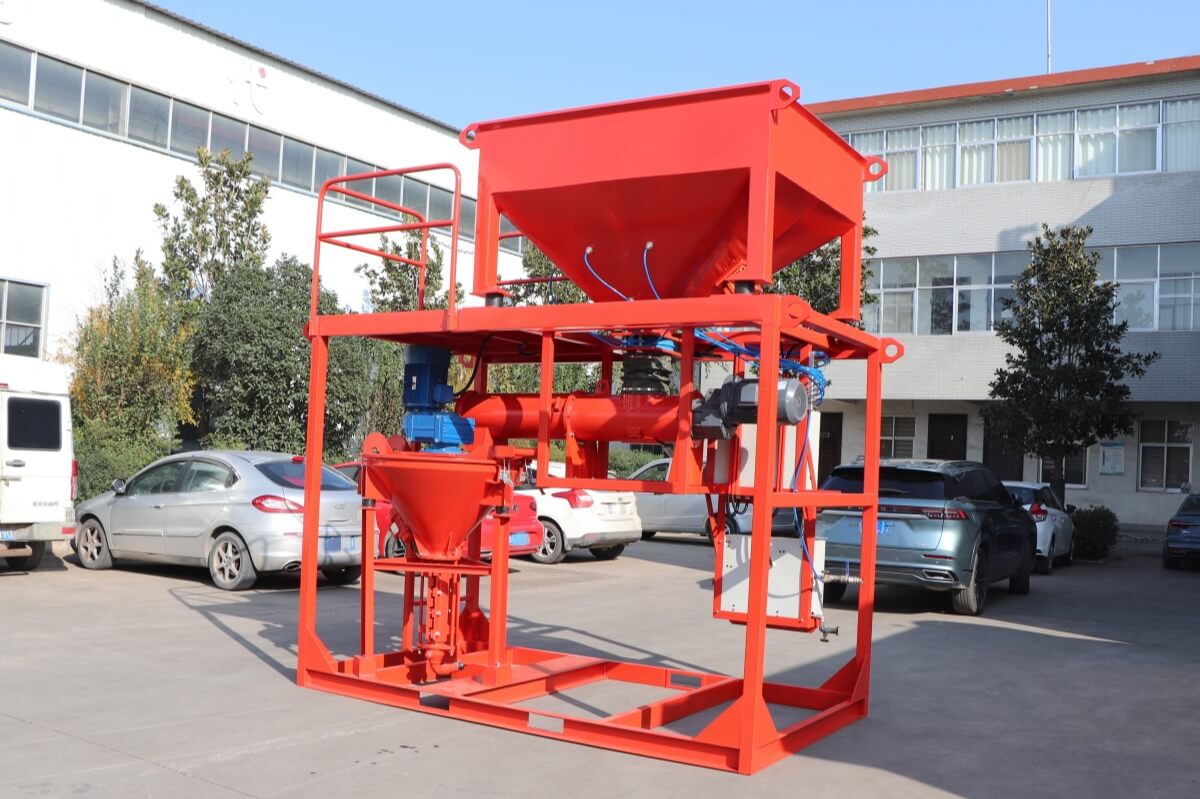